Solution & Vapor Deposition Precursors
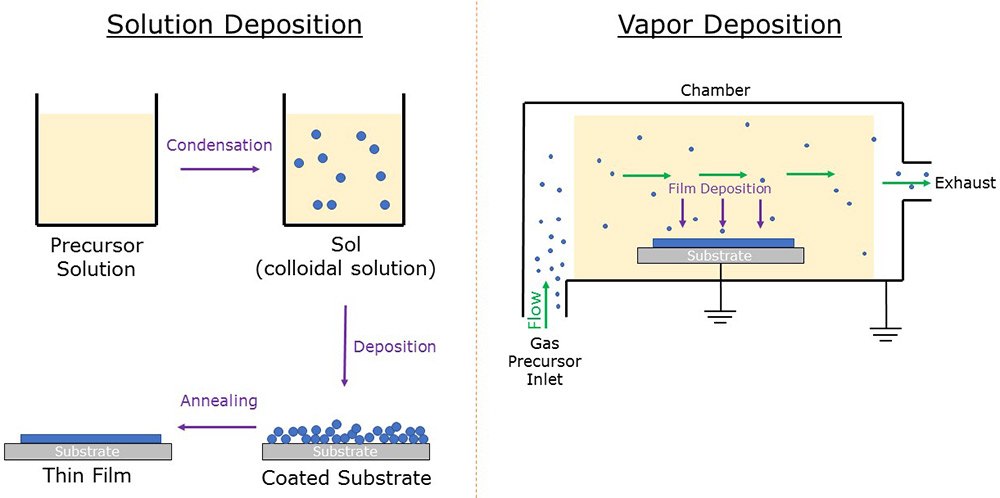
We offer an extensive range of high-purity Inorganic and organometallic chemicals specifically designed for solution processes, Chemical Vapor Deposition (CVD), Metal-Organic Chemical Vapor Deposition (MOVCVD) and Atomic Layer Deposition (ALD) applications. Our materials are of high quality, with purities ranging from 99% to 99.9999%. This diverse selection of deposition precursors is designed to meet all your research needs, whether for bench-scale experiments, pilot-scale projects, or manufacturing. Our comprehensive portfolio includes:
|
|
Solution Deposition Precursors
The application of solution deposition precursors, commonly referred to as sol-gel precursors, has expanded significantly to encompass a variety of chemical processes. This method is now broadly defined as the creation of solid materials, including metal oxides, nanostructures, dense ceramics or glass, and thin films derived from precursor solutions. Our solution deposition precursors are engineered to provide unparalleled consistency and reliability by meticulously controlling trace metal impurities. We understand that maintaining high purity in sol-gel precursors is crucial for achieving the desired properties and functionality of the final materials.
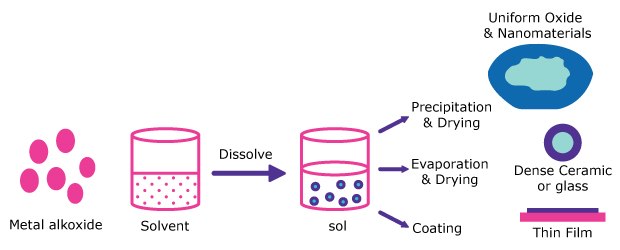
We offer 55 different base metals, featuring:
- Ultra-high purity trace metals ranging from 99.9% to 99.999% for superior research performance.
- Available functionalities such as acetate, acetylacetonate, tert-butoxide, isopropoxide, phenoxide, ethoxide, tri-sec-butoxide, methoxide, and 2-ethylhexanoate.
- Consistent quality with comprehensive specifications tailored for various applications.
- High solubility in appropriate solvents to facilitate the creation of homogeneous solutions for the sol-gel process.
Chemical Vapor Deposition (CVD)/Atomic Layer Deposition (ALD)
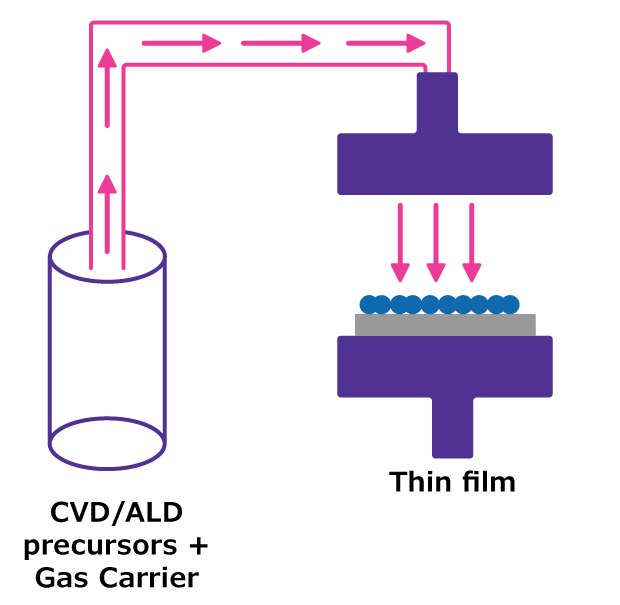
Atomic Layer Deposition (ALD) and Chemical Vapor Deposition (CVD) precursors play a pivotal role in the fabrication of nanometer-thin layers of metals, semiconductors, and insulating materials. These processes are vital for advanced electronics, efficient solar panels, memory devices, computer chips, and a variety of high-performance applications.
We recognize that selecting the appropriate precursors for CVD and ALD is essential for producing high-quality thin films. The chemistry of a precursor influences the film's composition, structure, and functionality. The critical factors such as purity, volatility, thermal stability, and reactivity with the substrate surface must be carefully evaluated, all of which affect the film's crystallinity, thickness, and surface morphology.
To address these needs, we provide high-purity precursors (99% to 99.999% trace metals basis) designed to minimize impurities that could adversely affect film properties. Our precursors are formulated to be thermally stable at deposition temperatures and reactive with the substrate, ensuring optimal film deposition. With these superior material qualities, we are committed to supporting your specific research and application requirements, enabling you to achieve precise and high-quality thin films.
Physical Vapor Deposition (PVD) Precursors
Physical Vapor Deposition (PVD) is a technique that employs vaporized material from solid sources to deposit thin films onto substrates. We provide high purity sputtering targets, pellets, metal foils, and evaporation slugs tailored for a wide range of PVD applications. These applications encompass microelectronic devices, battery electrodes, diffusion barriers, and optical coatings, ensuring high-performance outcomes across various industries.
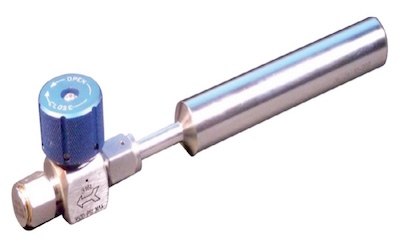
Precursors Packaged for Deposition systems
We offer high-quality ALD precursors that are safely and conveniently pre-packaged in robust steel cylinders, ensuring compatibility with a variety of deposition systems. Each cylinder is equipped with precision valves, allowing for controlled material flow into the deposition chamber, thereby enhancing operational efficiency and safety.
Applications
CVD is a leading technique in nanoelectronics, enabling the synthesis of high-quality nanomaterials essential for enhanced performance and miniaturization in electronic devices. CVD is widely used to produce carbon nanotubes (CNTs), boron nitride nanotubes (BNNTs), graphene, and metal oxides like SnO₂ and ZnO, which are critical for developing efficient, ultra-small devices.
Example: Two-dimensional (2D) transition metal dichalcogenides (TMDs) are particularly important due to their exceptional electronic and optical properties, with CVD playing a key role in growing high-quality thin films that optimize device performance, which is influenced by factors such as layer number, grain size, orientation, and morphology. CVD is instrumental in precisely growing these materials, ensuring optimal performance in various applications. Additionally, silicon carbide (SiC)-based nanomaterials are gaining traction for their superior mechanical, thermal, and electrical properties, suitable for various applications. Recent advancements in CVD and sol-gel processes have further enhanced the fabrication of SiC nanostructures, leading to high-performance devices like transistors and sensors capable of operating under extreme conditions.
In summary, CVD is a crucial technique driving advancements in nanoelectronics, renewable energy, and nanotechnology. It enables the precise creation of thin films and nanostructures, essential for high-performance solar cells, energy storage devices, and fuel cell components in renewable energy. In electronics, CVD facilitates the growth of materials for advanced transistors, sensors, and micro-devices. Additionally, it plays a vital role in synthesizing nanomaterials for applications like drug delivery and innovative materials. By addressing challenges in material synthesis and integration, CVD paves the way for future technological innovations.
Related Resources
- Brochure: High-Purity Materials for Molten Salt Applications
We offer a wide range of high-purity, low moisture salts in both powdered and beaded forms, with trace metal purities ranging from 99.9% to 99.999% as measured by ICP-MS or coupled ICP-OES.
- Brochure: Deposition & Semiconductor Materials
Explore our broad range of high-quality and dependable thin film deposition precursor and semiconductor materials as per your chosen method and application.
- High Purity Metalorganic Precursors for Concentrator Photovoltaic Technologies Device Fabrication
High Purity Metalorganic Precursors for CPV Device Fabrication
- Atomic Layer Deposition (ALD)
Atomic layer deposition (ALD) showcases innovation in novel structure synthesis, area-selective deposition, low-temperature deposition, and more.
- Group 11 Thin Films by ALD
Copper metal deposition processes are an essential tool for depositing interconnects used in microelectronic applications, giving group 11 (coinage metals: Copper, Silver, and Gold) an important place in atomic layer deposition (ALD) process development.
- Few Monolayer Atomic Layer Deposition (ALD) on Surfaces and Interfaces for Energy Applications
Few Monolayer Atomic Layer Deposition (ALD) on Surfaces and Interfaces for Energy Applications
- Silicon Nitride Atomic Layer Deposition: A Brief Review of Precursor Chemistry
atomic layer deposition (ALD), microelectronics, Mo:Al2O3 films, nanocomposite coating, photovoltaics, semiconductor devices, W:Al2O3 films, composite films, layer-by-layer
To continue reading please sign in or create an account.
Don't Have An Account?